Veolia Environmental saves money and improves vendor support at Pacific Northwest locations with the support of Pinmarx Connect software.
As one of the World’s leading environmental company’s, Veolia Environmental Services utilized Pinmarx Connect to service a regional Pacific Northwest fleet of light, medium and heavy-duty assets. The company transports hazardous waste and provides a full range of waste pick-up, disposal and recycling services. Currently operating a mixed fleet of assets that range from semi-trucks & trailers, to box-trucks and material handling equipment, Veolia Environmental has been able to submit requests via Pinmarx Connect and order services ranging from oil changes, engine work, towing and DOT inspections to lift-gate repair. This digital process improves asset utilization and safety.
Challenges
When Veolia began to look for a fleet coordination platform, they didn’t have a formal software program in place to schedule DOT’s, inspections and standard preventative maintenance. Many processes were being tracked manually through spreadsheets and other notification processes, but it wasn’t as simple and automated as they’d like.
Beyond the standard needs of tracking equipment costs, managing preventive maintenance, and tracking safety compliance, Veolia knew they needed software and vendor support services that would notify their management and schedule approved vendors with an agreed digital process. After reviewing other fleet management programs and DIY SaaS software on the market, the Pinmarx Connect platform ended up being the best overall solution for Veolia.
“The Pinmarx Connect program is the most complete, software, service provider support and tracking platform that identifies schedules and costs and improves operations and utilization,” said Eric Boze, Operations Manager at Veolia”
Solutions Provided
Veolia implemented the Pinmarx Connect software platform in 2013. To fit their needs, their regional locations were set-up with:
– 90 Day Scheduled Safety Inspections.
– 12 Month Federal Annual Inspections.
– Preventative Maintenance Scheduling.
– On-Site Mobile (LOF) Oil Change Services.
“We needed help tracking different parts of our fleet services prior to working with Pinmarx”, said Boze. “We have been able to track costs and maintain our rigid safety standards using Pinmarx Connect and their professional vendor network. Having a long term relationship over the years, has also allowed us to view costs, track repairs and limit the number of costly road calls each year.”
Excellent Results
Veolia has been involved with many improvements for their operations since the software and vendor support was implemented. One of the biggest impacts was completing safety inspections every quarter and tracking noted defects so smaller repairs didn’t turn into larger repairs while drivers were on routes. This process saved time & money. “We saved time & money within the first three service rotations by going through our records and reducing parts & labor costs by nearly 15%. All services were quoted with local vendors and Pinmarx provided us mobile on-site services or their vendor agreed to pick-up and deliver each asset” “That type of on-demand service was what we were looking for” said Mr. Eric Boze. “The ordering platform of Pinmarx Connect has been clearly a benefit to our organization and continues to make things flow and operate with ease. You can set scheduling parameters that are simple & easy to use. We’ve been able to manage our assets and standardize many of our own processes which meet our internal safety guidelines while Pinmarx helps us keep our vendors more accountable which reduces costs”, said Mr. Boze.
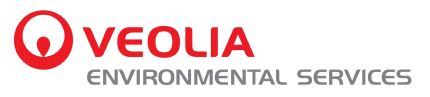
Industry
Environmental Services
# of Assets Managed at Branches
10+
Year Implemented:
2013
“We’ve saved more
than 15% by using
a professional platform that was experienced with our assets.”
– Eric Boze, Operations Manager Veolia Environmental
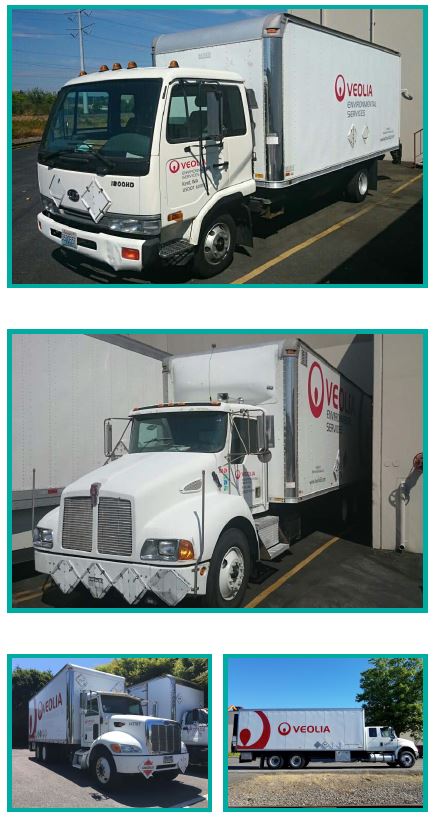